Registration/Grant of license under Factories Act 1948
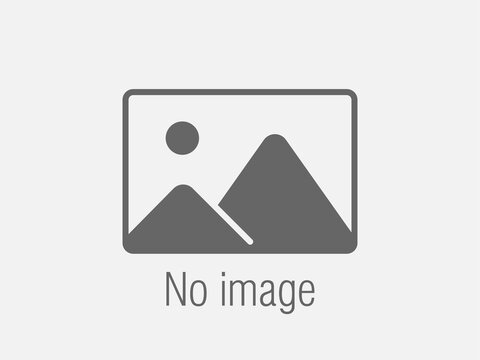
- info.sonydig
- Jun 4, 2024
- No Comments
Introduction to Registration/Grant of License under Factories Act 1948
The Factories Act of 1948 is a comprehensive statute that governs labor laws and ensures safety, health, and welfare of workers in factories across India. If you’re setting up a factory or running one, it’s crucial to understand the importance of registration and obtaining a license under this Act. This not only legitimizes your operations but also ensures compliance with essential safety and health standards aimed at preventing workplace accidents and illnesses. The registration and licensing process under the Act is designed to enforce industrial safety, regulate the employment of workers, and make the factory environment safer and healthier for everyone involved.
Overview of the Factories Act 1948
The Factories Act of 1948 is a critical legislation that governs the labor in factories and aims to ensure the safety, health, and welfare of the workers. Enacted shortly after India’s independence, this Act is an essential frame of reference for factory operations across the country, emphasizing the legal requirements that protect workers from industrial hazards and improve their working conditions. The Act applies to any premises where manufacturing processes are carried out with the aid of power and where ten or more workers are employed without power.
History and purpose of the Factories Act 1948
The Factories Act 1948 was instituted to replace the older Factories Act of 1934. The primary purpose of this legislation was to address the numerous concerns regarding the safety, health, and welfare of factory workers, which were inadequately protected under earlier laws. As industrialization progressed, the need for a comprehensive law became crucial, leading to the development and implementation of the 1948 Act. It introduced several vital regulations on working hours, safety measures, and the provision of amenities such as clean drinking water and restroom facilities at the workplace. At its core, the Factories Act aimed to mitigate the exploitation of labor and to institute a legal mechanism ensuring a safe and healthy working environment.
Registration under the Factories Act 1948
To establish and operate a factory in compliance with the Factories Act 1948, the owner must first undergo a rigorous process of registration. This is a fundamental step that not only legitimizes the establishment from a legal standpoint but also ensures that all the necessary safety measures are in place to protect the workers.
Requirements for registration
The registration under the Factories Act requires meticulous documentation and adherence to specific prerequisites. These include:
– A detailed factory layout plan showing the location of machines, firefighting equipment, and evacuation routes.
– Information on the number of workers employed and the nature of the work performed.
– Details about the use of raw materials, particularly hazardous chemicals and other dangerous elements.
– A description of the power supply and the type of machinery used in the factory.
– Proof of adherence to local and national environmental standards.
– Submission of documents verifying the installation of necessary amenities for worker welfare, such as washrooms, cafeterias, and medical facilities.
These documents and others requested by local governing bodies ensure that the factory is prepared to operate safely and in compliance with all applicable laws.
Procedure for registration
The procedure for registering under the Factories Act is straightforward but requires attention to detail. Here are the steps generally involved:
- Submission of Application: The factory owner must submit an application to the Chief Inspector of Factories. This application includes all the necessary documents, such as the factory layout and details about the machinery and workforce.
- Initial Inspection: Once the application is submitted, an initial inspection of the factory premises is usually conducted by officials from the factory inspectorate. They assess the safety measures, the working conditions, and the implementation of health facilities.
- Correction of Deficiencies: If any deficiencies are observed during the initial inspection, the factory owner must rectify these before proceeding. This could involve making structural amendments, upgrading machinery for safety, or improving the working conditions.
- Final Approval and Issuance of License: After compliance with all corrective actions and verification by the inspectors, the license to operate the factory is granted. The license must be renewed periodically, as specified by law.
By following these procedures, factory owners ensure not only legal compliance but also the safety and welfare of their employees, fostering a productive and secure working environment.
Grant of License under the Factories Act 1948
Understanding the licensing process
Obtaining a license under the Factories Act 1948 is a straightforward yet essential process for manufacturers intending to establish a factory. The first step involves submitting an application to the State Government or the Chief Inspector of Factories, which should detail the plans, specifications, and location of the factory. This application must comply with the requirements specified in the Act, focusing on safety measures, worker facilities, and environmental regulations. Following submission, an inspection of the proposed site is usually carried out by the authorities to ensure that all standards are met. If everything is in line with the Act’s provisions, the license is granted, which will need to be renewed periodically, as specified by the regulations.
Importance of obtaining a license
Securing a license for operating a factory is not just a legal formality; it’s a crucial step toward ensuring the legitimate functioning of an industrial establishment. A license signifies that the factory complies with several vital criteria:
– Legal Compliance: It verifies adherence to the law, preventing any legal actions or fines.
– Workplace Safety: It ensures that the factory adheres to safety protocols, which protect the workers from potential accidents and injuries.
– Business Reputation: Having a license enhances the credibility of the business, fostering trust among business partners and customers.
– Operational Continuity: It ensures uninterrupted operations by avoiding legal closures or disruptions due to non-compliance.
Compliance with industrial in safety standards
Adhering to industrial safety standards is not just critical for obtaining the license but for maintaining it over the years. Compliance involves regular inspections and audits, training employees on safety practices, and updating equipment and processes as per evolving safety norms. Under the Factories Act 1948, factory owners are obligated to provide a safe working environment that includes adequate lighting, ventilation, fire escapes, and emergency procedures. Regular drills, safety workshops, and health check-ups are encouraged to embed a culture of safety within the workplace. This not only minimizes the risk of accidents but also boosts worker productivity and morale, contributing to the overall efficiency and reputation of the factory.
Conclusion
Complying with the Factories Act 1948 is paramount for all factory owners, not only to adhere to legal standards but also to foster a responsible and safe working environment. Registration and obtaining a license under this act ensure that factories meet the required safety measures, which prevents legal repercussions and promotes the factory’s credibility. Moreover, compliance helps in reducing workplace hazards, ensuring a healthier working environment which is crucial for productivity.
The safety and welfare of workers should be the top priority for any industrial operation. Following the standards set by the Factories Act 1948 helps in:
– Protecting employees from occupational hazards,
– Providing adequate safety measures such as proper machinery maintenance and safety gear,
– Ensuring regular health check-ups and training sessions for workers.
By focusing on these areas, factories can create a safer workplace that not only enhances worker satisfaction but also boosts efficiency and productivity. Compliance is not just about following laws; it’s about valuing human life and well-being.
Prerequisite Documents:
Checklist of documents to be uploaded (Only png, jpg, pdf is supported and maximum file size of 4 MB is allowed)
Increase in Manpower
- Safety & health policy
- Extension plan details
- On site emergency plan
- Signature of occupier*
- Signature of manager*
Increase in Installed Power & Change in Manufacturing Process
- Safety & health policy
- Stability certificate*
- Extension plan details *
- On-site emergency plan
- SOP (Standard Operation Procedure) *
- SMP (Standard Maintenance Procedure) *
- Signature of occupier*
- Signature of manager*
Change in the Name of Factory
- Certificate of incorporation. *
- Memorandum and article of association
- Search report (list of directors) *
- Resolution of the Directors if list of director changes *
- Court order*
- Govt. order in case of PSU
- Partnership formation/ dissolution deed*
- Resolution of partners about changes*
- Signature of occupier*
- Signature of manager*
Amendment is only applicable if increase in manpower and/ or installed power (K.W) or any change in manufacturing process or any change in the name of the factory. Based on the geographical location of the factory and no. of workers, application will be routed through the designated Officer.
Department
- Establishment of Machinery Banks for Custom Hiring
- Farmer profile updation
- Farmer Registration & Updation
- Mukhyamantri Krushi Udyoga Yojana (MKUY)
- National Food Security Mission (NFSM) - Support for Cultivation and Expansion of Oil Palm
- Special Fruit Specific Scheme
- Subsidy for Farm Mechanisation (farm machinery and implements) in selected Villages of Aspirational Districts
- Sugarcane Harvester for Custom Hiring
- Supply of Potato, Vegetables, and Spices Minikits at Subsidized
- Application for Insurance Coverage for Livestock
- Broiler Poultry Farming
- Construction of Growout Tanks
- Construction of New Ponds for Brackish Water Aquaculture
- Construction of Rearing Ponds
- Fish Transport Vehicles
- Issuance of Postmortem Reports and Insurance Documents for Insurance Claim of livestock
- Layer Poultry Farming
- Mini Poultry Feed Mill
- Motorisation of Traditional Crafts
- Popularization of Fisheries Machinery/Equipment
- Promotion of intensive aquaculture through biofloc technology
- Providing boats(replacement) and nets for traditional fishermen
- Registration of fishing boats(Marine)
- Registration of New Brackish Water Fish Farms
- Renewal of Fishing License
- Renewal of Registration of Brackish Water Fish Farms and Hatcheries
- Semi-Commercial Duck Farming
- Semi-Commercial Pig Farming
- Small Scale Poultry Hatchery
- Fire Safety Certificate for Building(s) or Premises
- Fire Safety Certificate for Temporary Structure
- Fire Safety Recommendation for Proposed Building(s)
- Fire Safety Recommendation for Temporary Structure
- Supply of Copy of Fire Certificate for Fire Incident in Insured Premises below 10 Lakh
- Supply of Copy of Fire Certificate for Fire Incident without Insurance
- Supply of Copy of Fire Report
- Amendment / Cancellation of Registration - Registration of Trade Union(M-18)-Labour(The Trade Unions Act, 1926 And Regulation, 1941)
- Amendment of Licence under Contract Labour Act
- Amendment of license under Factories Act 1948
- Amendment of RC under Orissa Shops & Commercial Establishments Act, 1956 And Orissa Rules 1958
- Amendment of Registration Certificate - Registration of Establishment(M-9)-Labour (The Building & Other Construction Workers (RE&CS) Act, 1996 and its Odisha Rules, 2002)
- Amendment/ Transfer of Registration - Registration of Motor Transport undertakings(M-12)-Labour (The Motor Transport Workers Act, 1961 And Orissa Rules, 1966)
- Ammendment of license under the Inter State Migrant Workmen Act 1979
- Ammendment of RC under Contract Labour Act
- Ammendment of RC under the Inter State Migrant Workmen Act 1979
- Annual Contributions
- Appeal for RC/license under the Inter State Migrant Workmen Act 1979
- Appeal for registration/Grant of license under Contract Labour Act
- Approval for extension plan for factories under Factories Act 1948
- Approval of erection permission for boilers under the Boilers Act 1923
- Approval of list of Holidays(M-16)-Labour(Odisha Industrial Establishments (National & Festival) Holidays Act, 1969 And Orissa Rules 1972)
- Approval of plan and permission to construct or take in to use of any building as factory under Factories Act 1948
- Approval of repair orders for boilers under the Boilers Act 1923
- Approval of steam pipeline drawings under the Boilers Act 1923
- Cancellation of License - The Beedi and Cigar Workers (CE) Act, 1966 And Orissa Rules, 1969
- Certification of Standing orders(M-17)-Labour (Industrial Employment (Standing Orders) Act, 1946 And Orissa Rules 1946)
- Death benefit
- Endorsement of Certificates of Boiler Attendants
- Endorsement of Welder's certificate
- Grant of Certificate for Manufacture of Boilers and Pressure Part Components - The Boilers Act, 1923
- Grant of Certificate of Registration - Registration of Trade Union(M-18)-Labour(The Trade Unions Act, 1926 And Regulation, 1941)
- Grant of Erector Certificate for Boiler and Steam pipelines - The Boilers Act, 1923
- Grant of Funeral expenses
- Grant of license for contractors under Contract Labour Act
- Grant of license for employment of migrant workmen in the recipient state under the Inter State Migrant Workmen Act 1979
- Grant of license for recruitment by the contractor in home state under the Inter State Migrant Workmen Act 1979
- Grant of license for recruitment by the local agent , who supply migrant workmen to the contractors of the outside state under the Inter State Migrant Workmen Act 1979
- Grant of Marriage assistance for marriage of Self / Dependent girl child
- Grant of Maternity benefit
- Grant of Repairer Certificate for Boilers and Steam pipelines - The Boilers Act, 1923
- Insured Person registration for Integrated Inventory Management System
- Intimation of BOE Certificate - Endorsement & Revalidation
- Modification of Standing orders(M-17)-Labour (Industrial Employment (Standing Orders)Act, 1946 And Orissa Rules 1946)
- Registration of boilers under the Boilers Act 1923
- Registration of Construction Worker
- Registration of Establishment - Registration of Motor Transport undertakings(M-12)-Labour (The Motor Transport Workers Act, 1961 And Orissa Rules, 1966)
- Registration of Establishment - The Beedi and Cigar Workers (CE) Act, 1966 And Orissa Rules, 1969
- Registration of establishment under Contract Labour Act
- Registration of establishment under the Inter State Migrant Workmen Act 1979
- Registration of Establishment(M-9)-Labour(The Building & Other Construction Workers (RE&CS) Act, 1996 and its Odisha Rules, 2002)
- Registration of RC under Orissa Shops & Commercial Establishments Act, 1956 And Orissa Rules 1958
- Registration/Grant of license under Factories Act 1948
- Reimbursement Claim of Medicine (RCM)
- Renewal of boilers and grant of short duration certificate under the Boilers Act 1923
- Renewal of Certificate for Manufacture of Boilers and Pressure Part Components - The Boilers Act, 1923
- Renewal of Erector Certificate for Boiler and Steam pipelines - The Boilers Act, 1923
- Renewal of License - The Beedi and Cigar Workers (CE) Act, 1966 And Orissa Rules, 1969
- Renewal of license of contractors under Contract Labour Act
- Renewal of license under Factories Act 1948
- Renewal of license under the Inter State Migrant Workmen Act 1979
- Renewal of Registration - Registration of Motor Transport undertakings(M-12)-Labour(The Motor Transport Workers Act, 1961 And Orissa Rules, 1966)
- Renewal of Repairer Certificate for Boilers and Steam pipelines - The Boilers Act, 1923
- Revalidation of Welder's certificate
- Transfer of license under Factories Act 1948
- Amendment of Byelaw of Registered Society (District level)
- Amendment of Registered Partnership Firm
- Amendment of the Bye-law of Registered Society (State Level)
- Apply for Conversion of Agricultural Land U/s 8(A) of OLR Act
- Apply for Demarcation (For Industries/Corporate Sectors only)
- Apply for Marriage Registration
- Apply for Mutation
- Apply for Partition of Land on Mutual Agreement U/s Sec 19(1)C of OLR Act
- Certified Copy of Previously Registered Deed
- Certify Copies of ROR
- Create UAI
- Dissolution of Partnership Firm
- Dissolution of Society
- Issuance of Caste Certificate
- Issuance of Guardianship Certificate
- Issuance of Income & Asset Certificate
- Issuance of Income Certificate
- Issuance of Legal Heir Certificate
- Issuance of OBC Certificate
- Issuance of Residence Certificate
- Issuance of SEBC Certificate
- Issuance of Solvency Certificate
- Issuance of Tribe Certificate
- Issue of Encumbrance Certificate
- Registration of Documents (Submission)
- Registration of Partnership Firm
- Registration of Society (where more than one district is involved -State Level Society)
- Registration of Society (where one district is involved)
- Issue of Certificate Verification (CHSE)
- Issue of duplicate copy of High School Certificate
- Issue of duplicate copy of the High School Mark sheet by Board of Secondary Education, Odisha.
- Issue of Migration Certificate
- Issue of Original High School Certificate –cum-Mark sheet by the Board of Secondary Education, Odisha
- Issue of Pass /Equivalence Certificate
- Issue of verification of Mark Sheet by CHSE
- Readdition of Marks on Manual Valuation (CHSE)
- Readdition of Marks on Screen Valuation (CHSE)
- Renewal of affiliation to the Colleges by CHSE
- Authentication of certificates under World Educational Society Employers (VSSUT)
- Duplicate / Name Correction Degree Certificate (BPUT)
- Duplicate / Name Correction Grade Sheet (s) (BPUT)
- Duplicate Degree Certificates (VSSUT)
- Duplicate of Printed Provisional Pass Certificate (CET & IGIT Saranga)
- Duplicate of Printed Provisional Pass Certificates (VSSUT)
- Final Exam Grade Sheet (CET & IGIT Saranga)
- Final Exam Grade Sheets (VSSUT)
- Migration Certificate (BPUT)
- Migration Certificate (VSSUT)
- Online Final Grade Sheet (s) (BPUT
- Online Provisional Pass Certificate (BPUT)
- Online Provisional Pass certificates (VSSUT)
- Online Semester Grade Sheet (s) (BPUT)
- Photocopy of used answer Booklet (s) by E-Mail (BPUT)
- Photocopy of used Answer Booklets (by-Email) (CET & IGIT Saranga)
- Photocopy of used Answer Booklets(by e-mail) (VSSUT)
- Provisional Certificate (CET & IGIT Saranga)
- Semester Grade Sheet (CET & IGIT Saranga)
- Semester Grade Sheets (VSSUT)
- Transcript (CET & IGIT Saranga)
- Transcript (s) (BPUT)
- Transcript (VSSUT)
- World Education Services (Academic Records Request Form) (BPUT)
- Admission of Disabled students in Special School
- Free laptop for students
- Online Application and issuance of PwD ID Cards
- Online Application and sanction of Marriage Incentives
- Online Application for MBPY Pension Scheme
- Online Application for NSAP Pension Schemes
- Online Application for Scholarships
- Online Grievance lodge system
- Online Registration for BBSA Camp
- Online Registration for NGOs
Related Blogs
-
Renewal of Repairer Certificate for Boilers and Steam pipelines – The Boilers Act, 1923
-
Grant of Repairer Certificate for Boilers and Steam pipelines – The Boilers Act, 1923
-
Renewal of Erector Certificate for Boiler and Steam pipelines – The Boilers Act, 1923
-
Grant of Erector Certificate for Boiler and Steam pipelines – The Boilers Act, 1923